

This review outlines the key consideration for the fabrication of MLMM electronics and highlights the potential of 3D printing for future generation of electronics. However, the fabrication of MLMM electronics is challenging as various design and fabrication considerations need to be taken care of. 3‐dimensional printing of multilayered and multimaterials (MLMM) electronics has opened new opportunities for unconventional electronics. In particular, the focus will be placed on discussing the interface conditions between different materials such as surface wettability, surface roughness, material compatibility, and the considerations for postprocessing treatments. As such, this review aims to summarize the current landscape of 3D printing of MLMM electronics and provide some insights on the design consideration, fabrication strategies, and challenges of 3D printing of MLMM electronics. Despite these many works, there has been no review on the design and fabrication consideration for the 3D printing of multilayered and multimaterial (MLMM) electronics. which involve multilayer multimaterial printing.
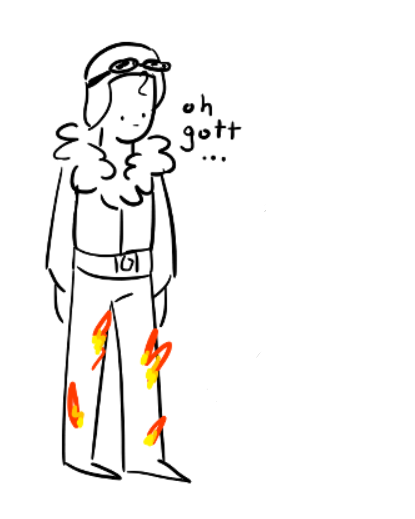
Recently, there are many works involving the use of 3D printing fabrication techniques for advanced electronic components and devices such as parallel plate capacitors, inductors, organic light‐emitting diodes, photovoltaics, transistors, displays, etc. Initially, 3D printing is used for the fabrication of electronic components with single material designs such as resistors, inductors, circuits, antennas, strain gauges, etc. With the advancement in materials and manufacturing technology, 3D printing has found its applications in the field of electronics manufacturing. to pattern the source-drain electrodes for all-inkjet-printed thin-film transistors.ģD printing, also known as additive manufacturing, is a manufacturing process in which the materials are deposited layer by layer in an additive manner. This novel approach turned out to be a fast and reproducible high-resolution patterning process for multiple applications, e.g.
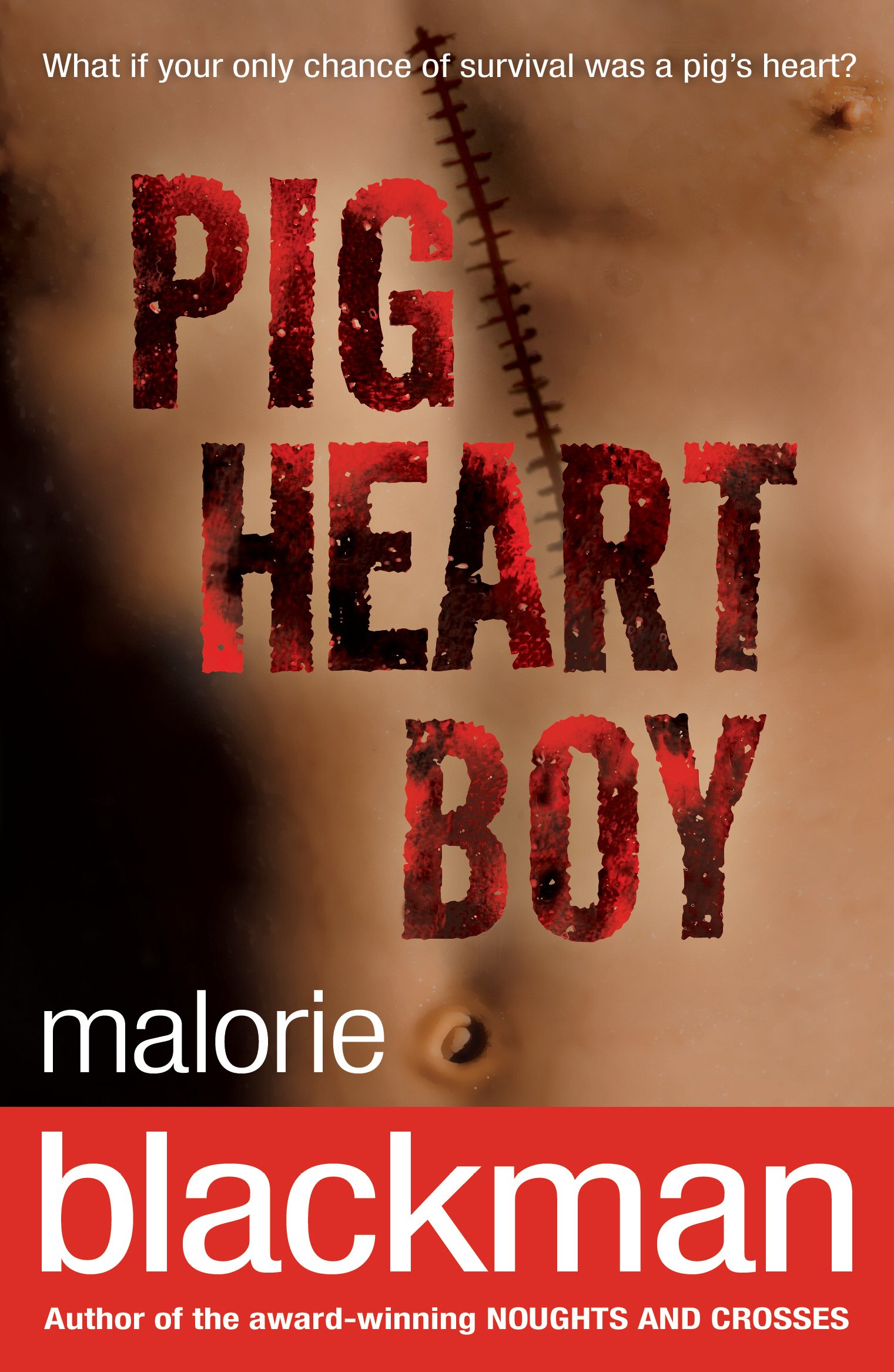
Careful optimization of the IPL parameters allowed to adjust the lateral width of the crack.
Photo print pilot crack crack#
The crack formation is controlled by selection of the substrate material, the fine-tuning of the morphology of the silver layer and an application of a dielectric layer on top of the silver layer that acts as a stress concentrator. The patterning is obtained by induced and controlled crack formation in the thin silver layer due to the intense exposure of IPL. In this contribution, IPL is used for the fine-patterning of printed silver nanoparticle layers. manufactured via roll-to-roll (R2R) processing. IPL was found to be a very fast and substrate-gentle approach qualified for the field of flexible and large-area printed electronics, i.e. During the last years, intense pulsed light (IPL) processing has been employed and studied intensively for the drying and sintering of metal nanoparticle layers deposited by means of printing methods on flexible polymer substrates.
